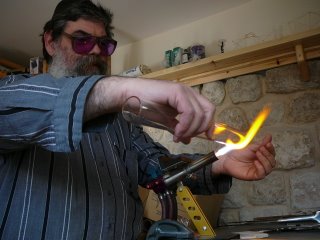

In town today: glassblower Joe from N.Y. area,once again lighting up the neighbourhood with molten boro-silicates.
Me? Still taking it easy: made and bisc'ed a bunch of pots for Meir's Purim anagama,some of which I sent to Ricardo for his wood/salt firing next week.It'll be interesting to see the results of the same group of pots fired in different wood kilns.I should put a couple aside for the next Tel Hai anagama. Most of the sinks I made for attempted crystal firing cracked in the bisc,but one of the survivors is currently basking in 1262 degrees of heat [a couple of degs. from the height of the firing,after which the crystalising part begins].Meanwhile,I am attempting to deflocculate some earthenware , searching for the elusive terra sigilata [sealed earth] used by potters for thousands of years to get a shiny finish without a glaze.I've never done this before,so it's about time. One batch of earthenware seems to be separating out nicely,another one hasn't moved.A batch of ball-clay also looks promising.
By the way,I think I might have found a way around that habit the blog has of sticking the first word of a posting way up in the right corner- the solution being to place the picture in the middle,instead of on the right.Simple,really.Took me a year to work it out.